SSI’s Technology
At SSI, our success and growth are based on the technologies we use. We work hard to help our clients to create the best shredding machines possible. Our machines are built to be durable, quick, and capable of handling challenging materials; they are covered by patents.
Our engineers are well-versed in finding unique and rare approaches to complex and challenging issues and problems. Our technology provides ultra performance and dependability whether you're handling waste, recycling, safeguarding items, or preparing materials. We are committed to ensuring you get the most out of your shredder.

Traditional locking methods for shredder cutters and spacers often lead to gradual loosening during operation, resulting in frequent maintenance, potential damage, and reduced performance. This conventional approach requires regular, tedious adjustments to keep the system functioning properly.
SSI has engineered a superior solution with our patented Advanced Cutter Locking System (ACLS) technology. ACLS securely locks the cutters and spacers onto the shaft, preventing any loosening during operation.
By eliminating the need for shaft threads, the ACLS pre-load hub assembly uses a series of sequentially tightened bolts, secured to the shaft with a segmented locking ring, to apply an impressive force of approximately 100,000 lbs. (45,000 kg) to the end of the cutter stack—nearly 850% more than standard threaded nut arrangements, which typically provide only 10,000 - 15,000 lbs. (4,500 - 6,750 kg) of force.
This increased stack loading creates a tighter and more secure cutter stack, enhancing cutter performance and significantly reducing the risk of shaft damage or failure. Operators and maintenance personnel greatly benefit from ACLS, as it virtually eliminates the need for frequent cutter stack tightening, resulting in substantial time and cost savings.
Learn more about our ACLS™ Advanced Cutter Locking System in the following video: SSI Technology - ACLS™
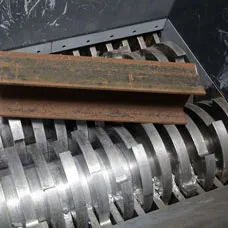
All SSI shredders are equipped with an advanced control feature that automatically reverses the operational direction when necessary. This function helps reorient the material, enhancing the machine’s ability to efficiently grab and process it.
If the material cannot be processed after a pre-set number of attempts, the controls will automatically halt the shredder, triggering the shredder horn to indicate the machine has stopped. To learn more about how our electric and hydraulic drives respond to reversals, explore our informative videos: SSI Technology - Electric Drives and SSI Technology - Hydraulic Drives.
Learn more about our electric and hydraulic drives and how they react to reversals in the following videos: SSI Technology - Electric Drives or SSI Technology - Hydraulic Drives
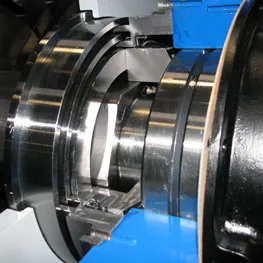
At SSI, our industrial shredders are engineered precisely to maximize online reliability and minimize contamination. Our cutting chamber design is a key element in achieving these goals. By strategically isolating system bearings and seals from processed material, we prevent seal damage and enhance the durability of our shredders.
Each SSI shredder features innovative splash plates, also known as false end plates, positioned at both ends of the cutting chamber. These splash plates effectively separate shredded material from the seal area, ensuring that the seals remain protected.
To further reinforce this barrier, we utilize round, hookless cutters adjacent to the splash plates, preventing any shredding directly against the splash plate walls. Additionally, a precisely calculated radial clearance between an oversized spacer and the splash plate opening provides an extra layer of protection.
For applications requiring minimal contamination and optimal online reliability, SSI's shredders are designed with a specialized space between the splash plates and the shredder end walls. This capped space, featuring an open bottom, allows any material that bypasses the splash plates to fall to the floor, safeguarding the shredder seals.
For select applications, we also offer advanced bearing and seal arrangements, including labyrinth seals, Teflon seals, and other custom designs tailored to your specific needs.
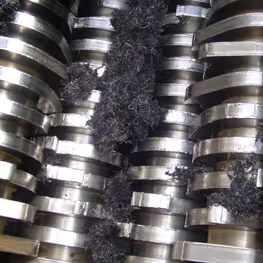
At SSI, our industrial shredders are engineered precisely to maximize online reliability and minimize contamination. Our cutting chamber design is a key element in achieving these goals. By strategically isolating system bearings and seals from processed material, we prevent seal damage and enhance the durability of our shredders.
Each SSI shredder features innovative splash plates, also known as false end plates, positioned at both ends of the cutting chamber. These splash plates effectively separate shredded material from the seal area, ensuring that the seals remain protected.
To further reinforce this barrier, we utilize round, hookless cutters adjacent to the splash plates, preventing any shredding directly against the splash plate walls. Additionally, a precisely calculated radial clearance between an oversized spacer and the splash plate opening provides an extra layer of protection.
For applications requiring minimal contamination and optimal online reliability, SSI's shredders are designed with a specialized space between the splash plates and the shredder end walls. This capped space, featuring an open bottom, allows any material that bypasses the splash plates to fall to the floor, safeguarding the shredder seals.
For select applications, we also offer advanced bearing and seal arrangements, including labyrinth seals, Teflon seals, and other custom designs tailored to your specific needs.
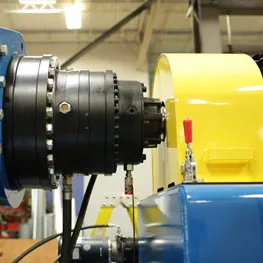
At SSI, we provide both electric and hydraulic drive options for our industrial shredders, including our advanced two-shaft shredders. Our direct drive systems are designed for optimal efficiency, featuring a high-efficiency, force-balanced planetary gearbox.
This gearbox offers both speed reduction and torque amplification, which are essential for heavy-duty shredding applications, such as tire shredding. One of the standout features of SSI shredders is the integration of the planetary gearbox directly onto the drive shaft. This design not only simplifies the drive system but also offers several standard gear ratios.
This flexibility allows operators to easily adapt to changing shredding requirements by adjusting the speed and torque combinations in the field. The heavy-wall construction of our shredders provides robust support to the drive train components, ensuring superior load handling and long-term reliability.
Additionally, our straightforward two-gear drive train is designed for ease of maintenance, with quick-access gearbox covers that make inspections simple and efficient. In contrast, indirect drive systems, often found in other shredders, connect the hydraulic motor or reducer to an input shaft via a mechanical coupling.
These systems typically involve complex four- or five-gear drive trains, which can lead to unbalanced force distribution, uneven wear on components, and reduced overall efficiency. Moreover, the large, multiple gears and difficult-to-access gearboxes in these systems can significantly increase maintenance and operating costs.
Learn more about our electric and hydraulic drives and how they react to reversals in the following videos: SSI Technology - Electric Drives or SSI Technology - Hydraulic Drives
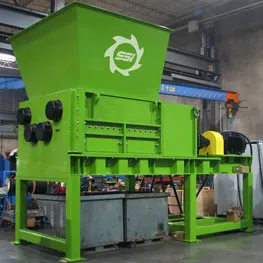
SSI shredding equipment using low-speed technology offer a variety of benefits. When used in conjunction with SSI’s auto-reverse and shock-load protection features, these shredders process a wide range of materials, including ferrous metal.
Power consumption is a key factor for many material processors today. SSI machinery is designed to minimize consumption by utilizing drives configured to application-specific criteria. SSI also offers an array of reduced voltage starting options for customers who are in an area where they are assessed off of peak current draw.
Low-speed shredders do not generate enough inertia to produce impact noise or large amounts of dust like higher speed machinery can. SSI shredders produce low noise levels and low dust emissions when compared to higher speed technologies. Vibration can cause stress fractures and component damage. Due to the low-speed design of SSIs shredders, these machines produce minimal amounts of vibration when compared to high-speed technologies which allow for no special foundation requirements.
SSI shredders are designed with large amounts of surface area to wear on consumable parts. When coupled with the low operating speed of the machine, this produces a recipe for long-lasting equipment with minimal downtime. These low-speed rotary shear shredders process baled, bulky or ferrous contaminated materials without special preparation, making them ideal preprocessors for a variety of high-speed equipment. SSI’s low-speed design incorporates programmable processing controls to aid metered feeding to downstream equipment.
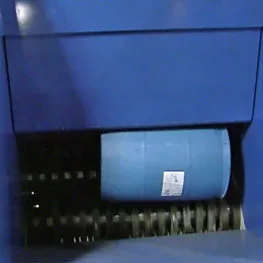
SSI’s Patented Ram Assist Technology addresses this issue head-on by pushing materials directly into the shredder, ensuring the cutter hooks can securely grab and process the material. Whether you’re dealing with challenging items like drums, plastics, steel, fiber, or even wooden pallets and C&D debris, the SSI Ram Assist delivers unmatched performance.
Operated hydraulically or pneumatically, this system is designed to maintain firm contact between the cutters and hard-to-grab materials, optimizing the shredding process for maximum efficiency. SSI’s Ram Assist is intelligently integrated with the shredder’s controls, compared to the brute plungers found on other shredders.
It senses when additional force is needed and adjusts accordingly, applying just the right amount of pressure and duration to ensure optimal material handling. This advanced system can be operated automatically or manually and is designed to sense cutter loading, retracting, or extending as necessary to maximize throughput.
SSI offers ram configurations tailored for a wide variety of vertical and horizontal feeding systems, making it an essential component in achieving superior results with your industrial shredder. Whether you’re processing materials for tire shredding, or handling bulky plastics, SSI’s Ram Assist Technology enhances performance and reliability every step of the way.
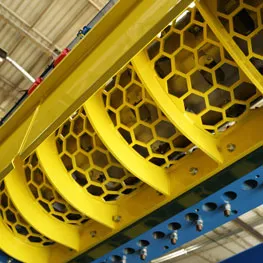
SSI’s innovative screen design is engineered to not only control particle size with precision but also enhance the shredding process itself. Our industrial shredder screens are concentrically aligned with the rotating cutter shafts, allowing the cutters to effectively interact with the screen face. This interaction tears and pulls apart materials with remarkable efficiency.
For instance, in tire shredding applications, the screen and cutter synergy efficiently liberates embedded metal beads and sidewall wires, preparing them for further processing. SSI’s shredder screens are designed with ease of installation and maintenance in mind.
To install or remove a screen, simply remove the end plate of the shredder, slide in the screen, adjust its height, and replace the cover plate. The screens are precisely designed to fit with SSI's cutter shafts, ensuring that the tolerance between the screen and the cutters can be adjusted to achieve optimal shredding results.
This compatibility makes our two-shaft shredders not only highly effective but also user-friendly, reducing downtime and maintenance efforts.
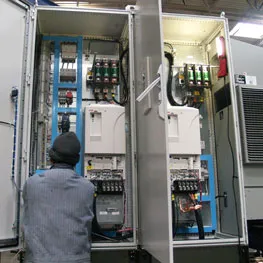
At SSI, we developed SmartDrive technology to enhance the performance of traditional electric and hydraulic drive systems. With SmartDrive, traditional electric drive applications can achieve unprecedented efficiency and power. Additionally, some hydraulic drive applications can now operate without the need for hydraulics, providing a more cost-effective and streamlined solution.
This advanced technology is available across all SSI electric drive shredders, offering superior performance in a wide range of shredding applications, including tire shredding and two-shaft shredding.
By utilizing the latest advancements in AC drive technology, SmartDrive® maximizes operational efficiency while significantly reducing operating costs. Whether you're dealing with the toughest materials or seeking to optimize your shredding processes, SSI's SmartDrive® technology offers a reliable, high-performance alternative that sets a new standard in the industry.
Learn more about SmartDrive® in our video overview, Technology: Electric Drives.

SSI’s SmartFeed is a patented method designed to optimize the processing of materials in our dual-drive industrial shredders. Available on a wide range of Dual-Shear®, Tri-Shear™, and Quad® shredders, SmartFeed™ ensures efficient shredding of even the most challenging materials—those that were once considered “impossible to process.”
This advanced technology enhances the performance of our two-shaft shredders, making them the ideal solution for tire shredding, waste management, and various other industrial applications.
Learn more about SmartFeed™ in our video overview, Technology: SmartFeed™.
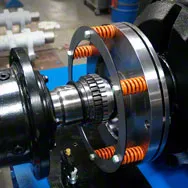
Component Details: While many industrial shredders come equipped with auto-reversal as a standard feature, not all of them provide true shock load protection for electric drives. At SSI, our electric drive shredders are designed with this essential technology built in as a standard feature.
In the event of a shock load situation, such as encountering a non-shreddable item, our Severe Shock Protection (SSP) technology prevents the increased torque from being transmitted directly to the shredder's drive train. This innovative feature safeguards the system, protecting critical components like the cutters, shaft, and drive train from potential damage.
By extending the lifespan of these vital parts, Severe Shock Protection enhances the overall reliability and durability of our shredders, ensuring your operation continues to run smoothly and efficiently.
Watch our Technology: Severe Shock Protection™ video to learn more.
Ready to start shredding?
Our team is standing by to help you find the ideal shredding solution for your company.