3 Ways to Shred
Shearing
This action involves the actual cutting of material. As in scissors, shearing efficiency depends on the sharpness of the cutting edges working against each other and the tolerance of the space between them. SSI has developed technology (such as ACLS and hardened alloys) to maintain this tolerance and sharpness, ensuring a clean cut even after long operation.
Tearing
Tearing involves pulling the material with such force that it comes apart. Some materials like fabric, soft metals, plastics, and tires, are more tearable than others. Purpose-built tearing reducers (such as SSI's Primary Waste Reducers) are good for reducing mixed waste where small, uniform particle size is not important.
Fracturing
Some materials are brittle, such as glass, hard plastics, and certain metals, and tend to be broken or shattered in a shredder when the cutters aren't sharp or are loose. Unlike tearing, when something breaks it releases energy explosively, sometimes propelling the shards upwards into the faces of the fascinated onlookers. Always wear eye protection.
Optimum Action
All three actions, shearing, tearing, and breaking are present when a shredder is being used. However, when the cutters are kept sharp and the tolerances tight, the dominant and most efficient reduction action should be shearing.
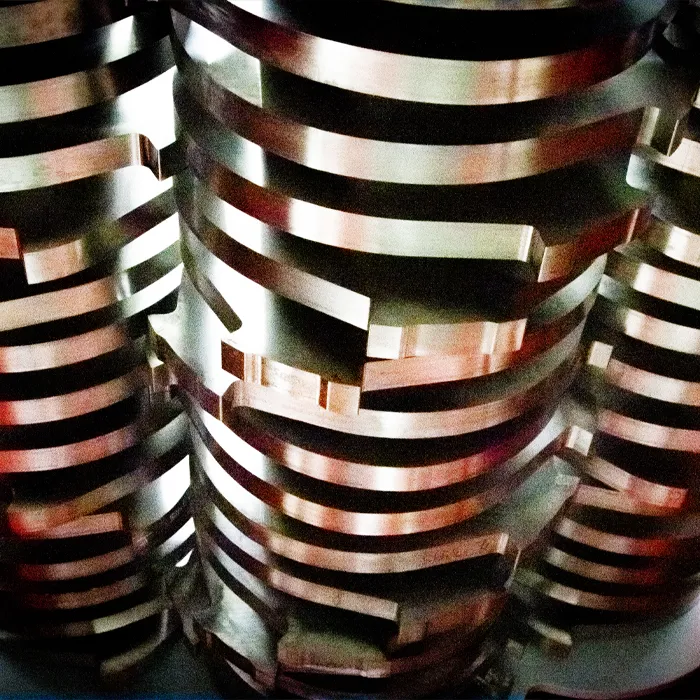
Grabbing
What is "Grabbing"
Grabbing is the ability of a shredder to seize the material and pull it down into the cutters. Grabbing is a function of the size and shape of the hook on the cutter and the size, as well as the weight and texture of the material coming into the shredder.
For instance a large, light, smooth object, like a plastic form, may be relatively easy to cut up but have a tendency to bounce or "float" on top of the rotating cutters. In this case it might be necessary to use a larger shredder or add a ram assist to push the material down into the shredder where it can be grabbed and pulled through.
A shredder should not grab more than it can shred.
There is a saying at SSI that a shredder should only grab what it can shred at one time. Some compressible materials, like carpeting or paper, can be grabbed too easily and can choke the shredder if too much is grabbed at a time. In such a case, one might reduce the hook height on the cutter so the shredder will only grab as much as it is designed for. One can also reduce the batch size or meter feed the shredder, controlling the rate of material going into the shredding table.

Shredder Types
SSI makes four basic types of high-torque shredders, each coming in various sizes and driven by either electric or hydraulic power units.
Uni-Shear®
Medium-speed, single-shaft, rotary grinder. Recommended for uncontaminated wood, paper, hard plastics, and brittle materials where small, uniform particle size is vital.
Learn more »
Dual-Shear®
Low-speed, high-torque, two-shaft, shear shredder. Recommended for metals, soft plastics, tires, product destruction, or any diverse and contaminated materials where particle size variation is allowed.
Learn more »
Quad®
Low-speed, high-torque, four-shaft shredder specially suited for applications such as e-scrap, tires, alternative fuel production, and other materials where uniform, small to medium particle size is desired.
Learn more »
PRI-MAX®
Low-speed, high-torque, multi-material primary reducer. A high-capacity solution ideal for construction and demolition and for volume reduction of bulky waste containing metal and abrasives. Particle size is coarse.
Learn more »
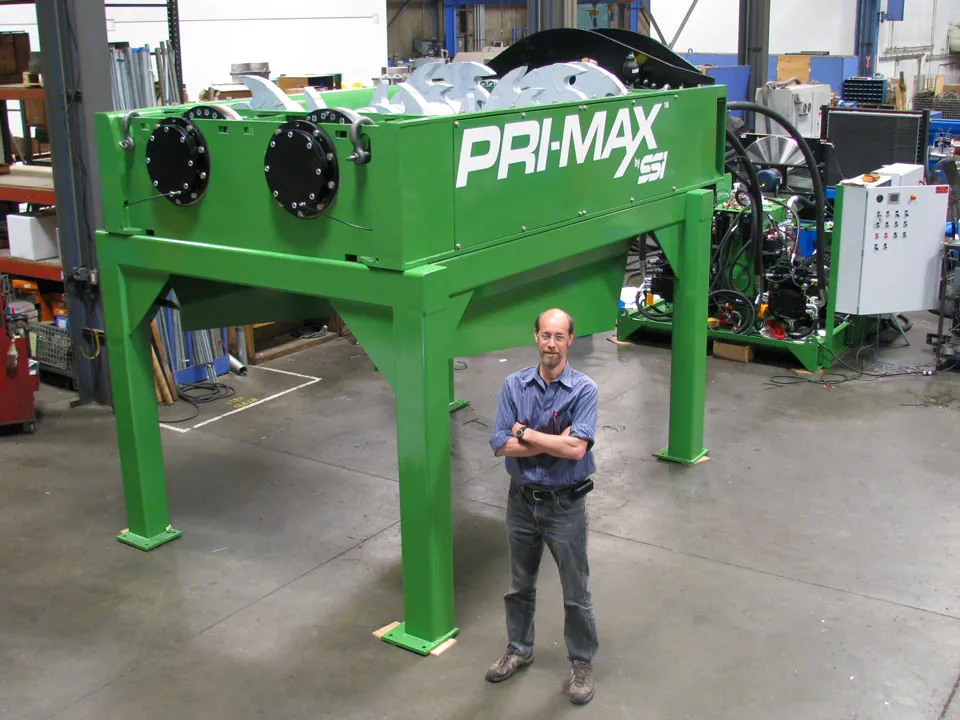
Shredder Sizing
The right sized shredder is important. SSI will, as a rule, recommend a shredder that is sized to need much less than 100% of its available power to do the job.
The reason for this is that as cutters dull with use, they require more power to shred. With an ample reserve power capacity, the performance of a shredder can be maintained for far longer before the cutters need to be replaced.
SSI also recommends that a shredder be sized to grab only as much material as it has the power to shred. So besides model size and power capacity, considerations like cutter and shaft dimensions, infeed chamber, and material properties need to be taken into account.
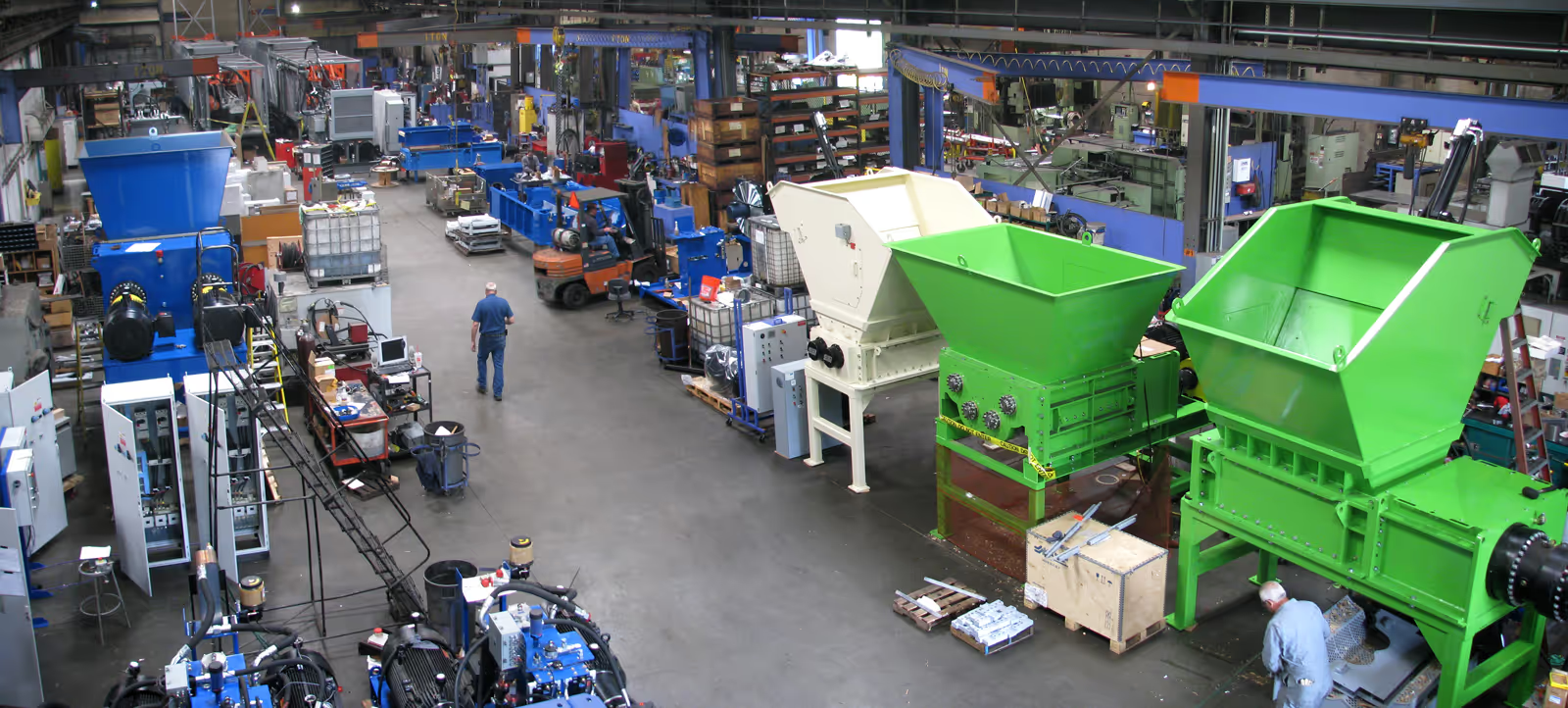
Feeding
Batch Feeding
Batch feeding involves dropping large masses of material into the hopper, either by some sort of grapple or loader. Batch feeding is common with appliance destruction, demolition work, or bale processing.
While batch feeding is simple and straightforward, it can also be inefficient. If not properly sized for the job, batch fed shredders are more likely to clog or take on more than they can shred at one time.
Meter Feeding
Meter feeding involves introducing material to the hopper in a steady, controlled stream, usually by conveyor. If a material can be meter fed, the shredder can monitor its own intake and operate more efficiently. Meter feeding can result in fewer reversals or shut downs.
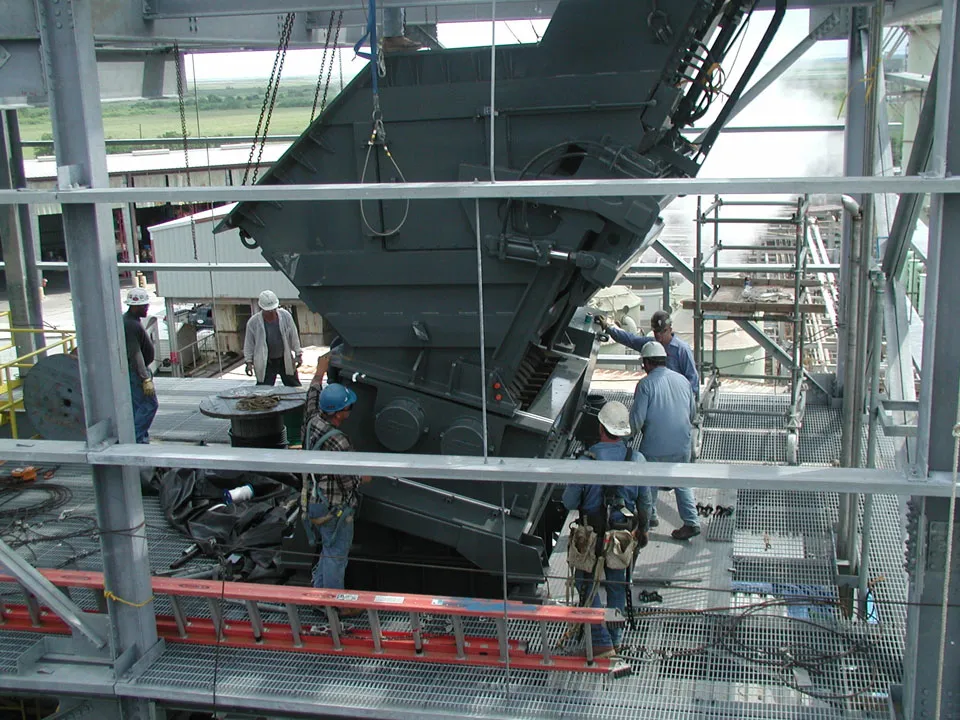
Electric or Hydraulic Drive
Electric Drives
Generally, electric shredders require less space, are easier to operate and maintain, and are more energy efficient than their hydraulic counterparts. They also tend to be less expensive. Electric shredders are appropriate and sufficiently powered processing many materials.
Hydraulic Drives
Hydraulic drives are often better for more heavy duty processing. They are also better for processing materials that experience frequent overloads from batch feeding. Hydraulic drives also offer better shock load protection from non-shreddables and work well with SSI's Auto-Chop feature, allowing more precise particle size control.
When would I need a hydraulic shredder?
A hydraulically powered shredder might be more appropriate if you have any of the following factors in your processing environment:
- Materials are batch fed.
- Feed include unsorted or unknown materials.
- Materials are exceptionally difficult to shred.
- Process requires tighter particle size control.
- System needs to meter shredded material to downstream equipment.
- System will require frequent starts and stops.
- Shredder will require reduced voltage start (soft start).
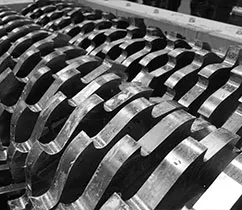
Pricing
SSI shredding systems can start for as little as $60,000 and into the millions, depending on the size, configuration, and overall scope of the integrated system.
One thing to consider when calculating price, however, is the lifetime cost of a shredder, including its maintenance, replacement parts, power costs, and expected useful life.
A final consideration in evaluating relative price is the payback time you should expect from your shredder. You can always find a unit that is cheaper in the beginning. But if it breaks down frequently, stopping your production line, it's actually costing you money.
SSI will work with your budget to build you the shredder that is the best solution for your operation.
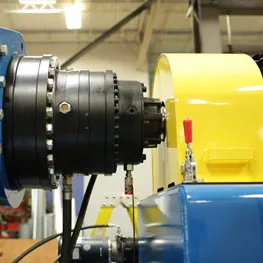
Industry Resources
May we suggest further resources for you to find more information about specific industries that use SSI shredders.
- General Recycling: National Recycling Coalition
- Tire Recycling: Tire Industry Association
- Mobile Document Destruction: National Association for Information Destruction
- Plastic Recycling: American Plastics Council
- Electronic Scrap Recycling: Institute of Scrap Recyclers Industries
- Solid Waste Recycling: The Solid Waste Association of North America
- Metals Recycling: Institute of Scrap Recyclers Industries
- Battery Recycling: Battery Council International
- Composting: U.S. Composting Council
- C&D Recycling: Construction Materials Recycling Association
Publications:
"Starting a Scrap Tire Company" from the Rubber Manufacturers Association

Ready to start shredding?
Our team is standing by to help you find the ideal shredding solution for your company.