How long can a machine really last? Apparently, forever, according to SSI Shredding Systems, located in Wilsonville, Oregon. SSI specializes in building solutions for waste and material processing. They really do build and service machines that last for a lifetime. This philosophy starts with every machine that they make, and have made, for 35 years.
SSI has installations in over 60 countries across the world and is actively involved in solving global waste challenges from medical and plastic waste to applications in Refuse Derived Fuels (RDF) and tire recycling. SSI learns from the past, and designs for the future, which is why their machines have such a long life. They listen to their customers, analyse that feedback, and create solutions. The result is a constantly improving product line.
As Max Neunzert, Senior Engineer at SSI puts it, “If a component fails to meet its design requirements, then my goal is to fix that. I don’t see any reason not to…. If I can make changes at the design level going into the product, right away, that eliminates problems 10 years later, we are going to make those changes,” says Neunzert.
A great example of this process can be seen through the evolution of the Uni-Shear® SR-500 machine. This product has seen numerous enhancements since it was first introduced in 1998.
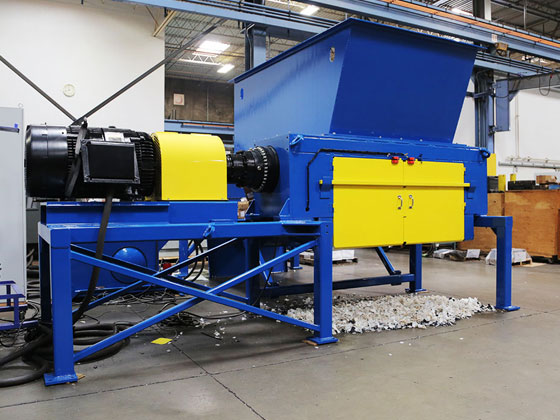
The Uni-Shear® SR-500 is a single-rotor shredder which is able to reduce bulky material in a single pass to create consistent, small-sized particles. The machine operates on very tight tolerances, and it’s this precision that makes it so powerful in many different applications.
The design has an intuitive ram feature, which senses the load on the shaft, through monitoring the amperage on the motor, and directing the pressure of the ram accordingly. This ram feature allows for consistent feeding of the material, maximizing efficiency of the shredding process.
One of their first redesigns included expanding the ram section dramatically (changing it from a square to a rectangular shape) to handle baled material and reinforce the design to withstand irregular forces and greater pressures.
After this modification, they were seeing some problems with the belts and the pulleys on the electric drive system, so they switched to a more efficient direct drive configuration.
These modifications done in the late 90’s and early 2000’s was really about taking the best features from two of their other product lines. They took their robust ram design from their compactors and the direct drive configuration from their line of Dual-Shear ® shredders.
Recently, in 2015, another breakthrough occurred when SSI received an order for a custom-built SR-500 that was going to be cutting some proprietary metal parts. SSI decided to modify the “angle of attack” between the cutters and the anvil to improve the cutting action. Not only would this change improve performance but ultimately create a machine that needs less repair and maintenance. SSI incorporated this modification into their main design for all SR-500s.
As Neunzert says, “Now we have a machine that is as bullet proof as we can make it. It has taken us 18 years to get to this point.”
Today, the Uni-Shear® can be configured for your specific application. The screens can be changed to vary particle size. The tolerances, cutter design, and anvil configuration can all be adjusted for your desired output.
“We don’t operate on the philosophy that we are going to put this machine out there and 5 years later it’s going to be trashed, and we are going to be selling them another one, it doesn’t work like that. Our customers come to us because they have a business model that says they are going to be processing for 99 years so why wouldn’t they want a machine that can process for 99 years?” says Neunzert.
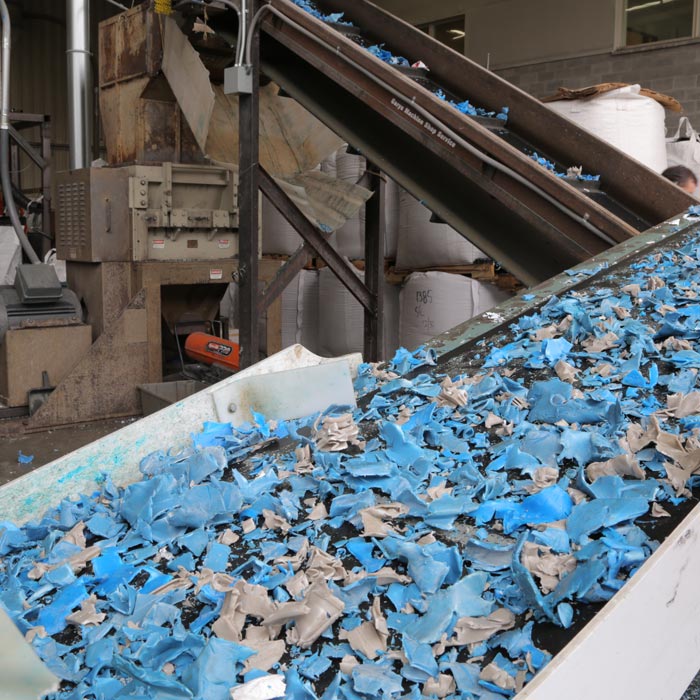
Subscribe to newsletter
Subscribe to receive the latest news & events to your inbox.