Kawasaki City, Kagawa Prefecture, Japan – Nihon Dust, a recycling and waste management company, is in its 53rd year of operation. Their long history does not mean they are old-fashioned. quite the contrary, Nihon Dust continues to adapt to the changing landscape of recycling.
“From [Nihon Dust’s] inception, we prioritized recycling and grew with the needs of the times,” states Jiro Yoshino the general manager of sales at Nihon Dust.
In September of 2023, Nihon Dust opened the Yako plant, a transfer and recycling facility specializing in difficult to process materials. Plastics, comingled metals, hoses, and fishing nets are among the types of waste that require special handling.
“The Yako Plant is a transfer station,” explains Haruhiro Sekiguchi, deputy plant manager of the Yako facility, “where we sort and process waste before it gets transported to its final processing site.”
Before incoming material can be effectively sorted and transported, first it must be shredded. However, shredding these materials can be a cumbersome and time-consuming process.
“Our old factory had a twin shaft shredder,” recounts Jiro Yoshino, “but before feeding it we had to cut large materials manually and the shredder jammed a lot.”
This inefficient process limited Nihon Dust’s capacity. So, while designing the Yako Plant, they searched for a better shredding solution. After exploring their options, they eventually reached out to Shredding Systems Inc (SSI), a shredder manufacturer known for its engineering and application expertise.
“[SSI was] very supportive and attentive in hearing our needs,” says Jiro Yoshino.
These conversations resulted in an innovative M120 EX Dual-Shear Shredder. The unique design stacks two low-speed, high-torque M120 two-shaft cutting chambers one on top of the other. Instead of a more conventional set up with two M120s connected via conveyors, the stacked design achieves the same results in half the space.
The top cutting chamber in the M120 EX delivers the primary shred, reducing infeed materials into strips that drop directly into the second cutting chamber. The secondary shred is important for making the material more flowable and compressible for efficient downstream sorting and transportation. The high throughput capabilities of the two-shaft design allow for a capacity of up to 70 tons in an 8 hour day.
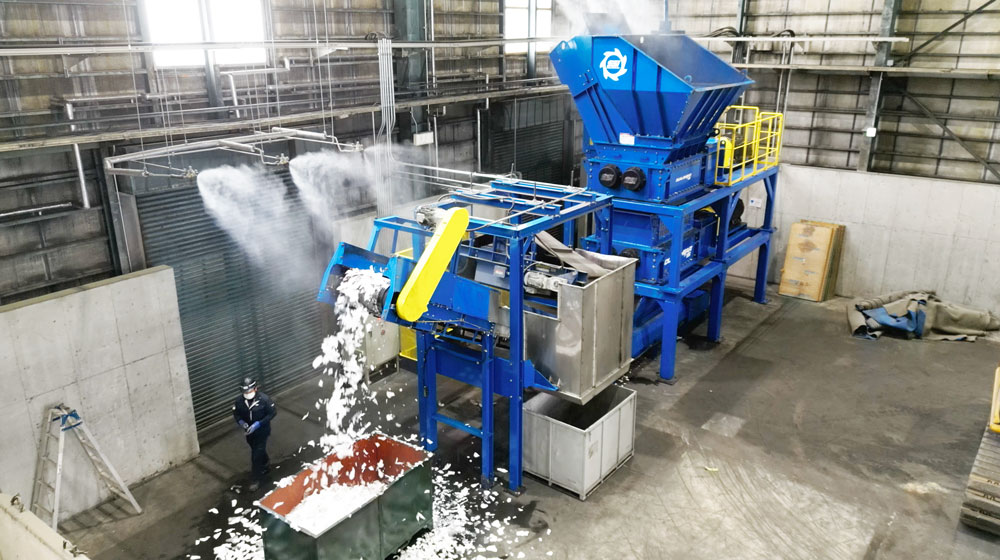
The M120 EX is an electric drive machine equipped with SSI’s patented SmartFeed® technology. SmartFeed® automatically monitors the shredder’s power usage and optimizes performance. If the material is tough, the machine will self-regulate using as much force as shredder can produce without overloading to digest the material. If the material is easier, speeds increase to maximize productivity. For a company like Nihon Dust, who encounter a variety of different hard-to-shred materials at one facility, this technology is crucial for maintaining production.
“Even materials which gave us a hard time in the past can now be shredded in a short amount of time,” says Takaomi Okuma, Yako Plant manager.
Nihon Dust recognizes the valuable roll they and other recyclers play in Japan’s push towards a circular economy and a future of environmental stability.
“Many of our customers are working on ‘Zero carbon by 2050,’” Jiro Yoshino concludes, “So the need to recycle is ever increasing.”
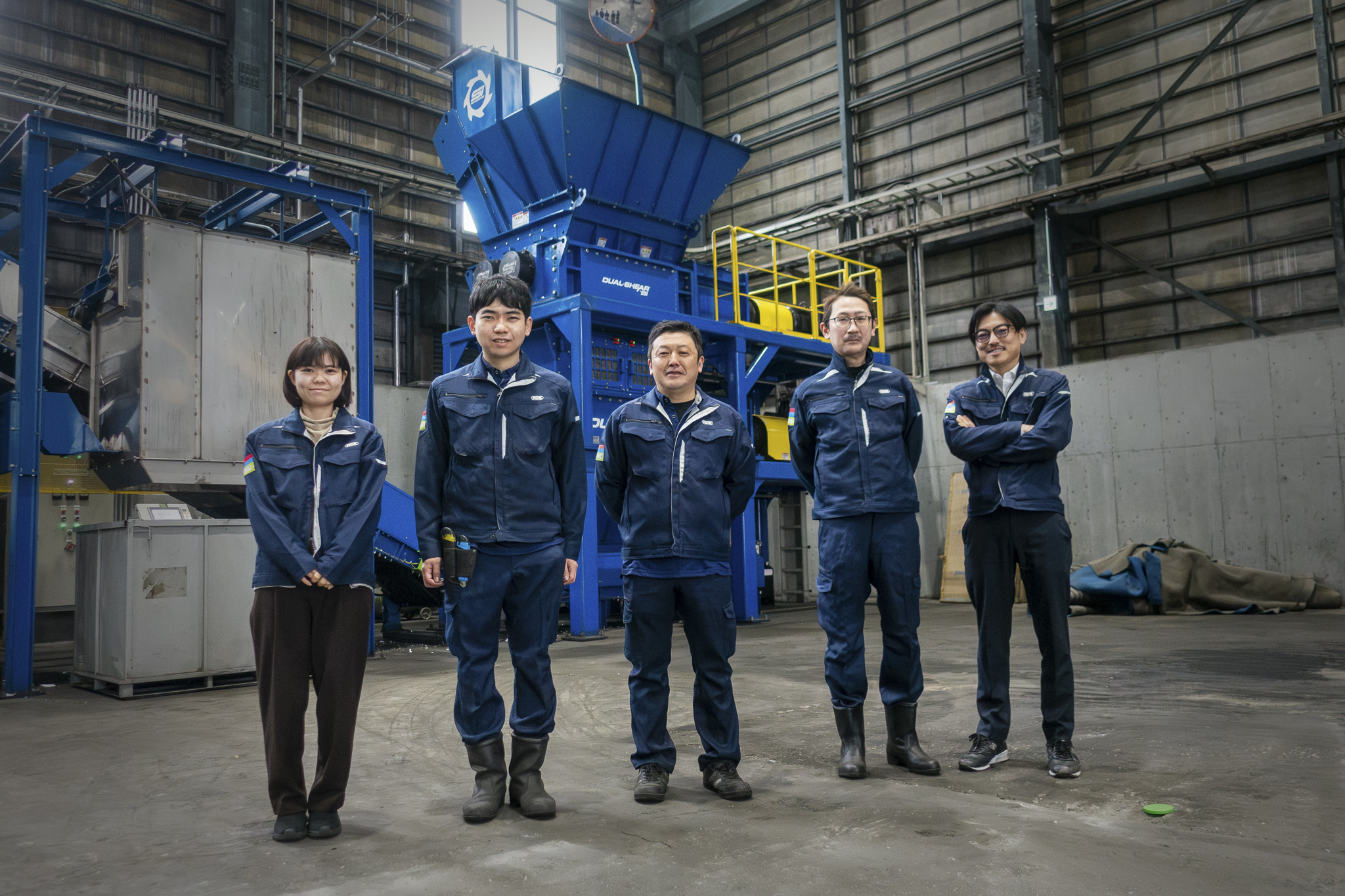
Subscribe to newsletter
Subscribe to receive the latest news & events to your inbox.